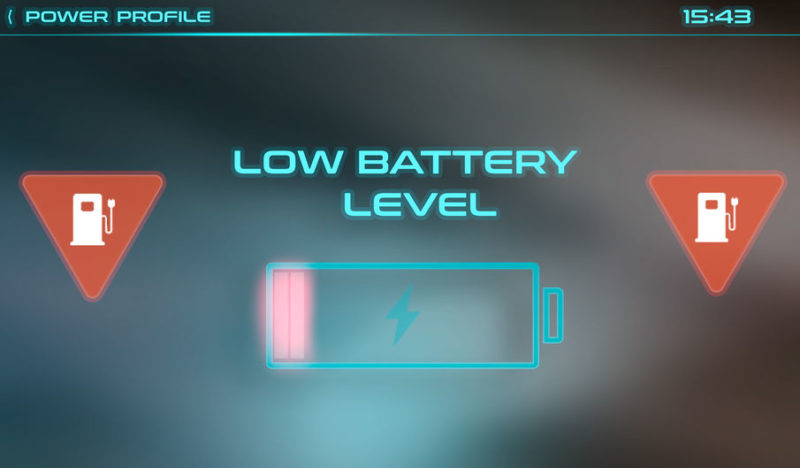
Weakest link to EV growth is the material supply chain
By Ronald Stein
The worldwide plans for EV domination of the vehicle population are like having the plans to build a large house without sufficient materials available to ever finish the house.
The pressure to go Green is increasing as countries are announcing plans to phase out petrol and diesel cars. Germany will stop the sale of all new petrol and diesel cars from 2030, Scotland from 2032, and France and the UK from 2040.
Even California, the current leader in America with 50 percent of the EV’s in country being in that state, has jumped onto the EV train with Democratic Governor Gavin Newsom, who will be on the 2021 Recall ballot, issued an Executive Order in 2020 to ban the sale of gas-powered vehicles in California by 2035.
A Tesla lithium EV battery weighs more than 1,000 pounds. While there are dozens of variations, such an EV battery typically contains about:
- 25 pounds of lithium,
- 30 pounds of cobalt,
- 60 pounds of nickel,
- 110 pounds of graphite,
- 90 pounds of copper,
Looking upstream at the ore grades, one can estimate the typical quantity of rock that must be extracted from the earth and processed to yield the pure minerals needed to fabricate that single battery:
- Lithium brines typically contain less than 0.1% lithium, so that entails some 25,000 pounds of brines to get the 25 pounds of pure lithium.
- Cobalt ore grades average about 0.1%, thus nearly 30,000 pounds of ore to get 30 pounds of cobalt.
- Nickel ore grades average about 1%, thus about 6,000 pounds of ore to get 60 pounds of nickel.
- Graphite ore is typically 10%, thus about 1,000 pounds per battery to get 100 pounds of graphite.
- Copper at about 0.6% in the ore, thus about 25,000 pounds of ore per battery to get 90 pounds of copper.
In total then, acquiring just these five elements to produce the 1,000-pound EV battery requires mining about 90,000 pounds of ore. To properly account for all the earth moved though—which is relevant to the overall environmental footprint, and mining machinery energy use—one needs to estimate the overburden, or the materials first dug up to get to the ore. Depending on ore type and location, overburden ranges from about 3 to 20 tons of earth removed to access each ton of ore.
This means that accessing about 90,000 pounds of ore requires digging and moving between 200,000 and over 1,500,000 pounds of earth—a rough average of more than 500,000 pounds of ore per battery.
According to Cambridge University Emeritus Professor of Technology Michael Kelly, replacing all the United Kingdom’s 32 million light duty vehicles with next-generation EVs would require huge quantities of materials to manufacture 32 million EV batteries:
- more than 50 percent of the world’s annual production of copper.
- 200 percent of its annual cobalt.
- 75 percent yearly lithium carbonate output; and
- nearly 100 percent of its entire annual production of neodymium.
One can easily see that the world may not have enough minerals and metals for the EV batteries to support the EV growth projections roadmap when you consider that today:
- Combined worldwide car sales in 2019 were more than 65 million vehicles annually.
- There are 1.2 billion vehicles on the world’s roads with projections of 2 billion by 2035.
Today, there are less than 8 million EV’s operating on the world’s highways. If EV projections come to reality by 2035, 5 to 7 percent of the 2 billion vehicles would equate to 125 million EV’s on the world’s roads, and potentially double that number if governments step up the pace of legislative change. However, looking at the UK study of the materials required for only 32 million EV batteries, there may not be enough materials in the world to finish the EV conversion plans.
Further bad news is that a single digit penetration into the worlds projected 2 billion vehicles would also represent more than 125 BILLION pounds of lithium-ion batteries, just from those 125 million EV’s that will need to be disposed of in the decades ahead.
Zero and low emission vehicles are generally from the hybrid and electric car owners which are a scholarly bunch; over 70 percent of EV owners have a four-year college or post-graduate degree. This likely explains why the average household income of EV purchasers is upwards of $200,000. If you are not in that higher educated echelon and the high-income range of society, and a homeowner or resident of a NEW apartment that has charging access there may not be an appetite for an EV.
A recent 2021 California study shows that EV’s are driven half as much as internal combustion engine vehicles which further illustrates that EV’s are generally 2nd vehicles and not the primary workhorse vehicle for those few elites that can afford them.
Getting back to those plans to build a large house with an insufficient supply of materials to ever complete the house, maybe we should learn from the UK study of the materials required for only 32 million EV batteries (less than 7 percent of 2 billion vehicles in 2035) and set our sights on achieving an EV population that the world’s supply of the minerals and metals can support.
Author
Ronald Stein is an engineer who, drawing upon 25 years of project management and business development experience, launched PTS Advance in 1995. He is an author, engineer, and energy expert who writes frequently on issues of energy and economics.
From cfact.org